Estrategias de diseño de bombillas LED de alta luminosidad y bajo coste, compatibles con casquillo E27
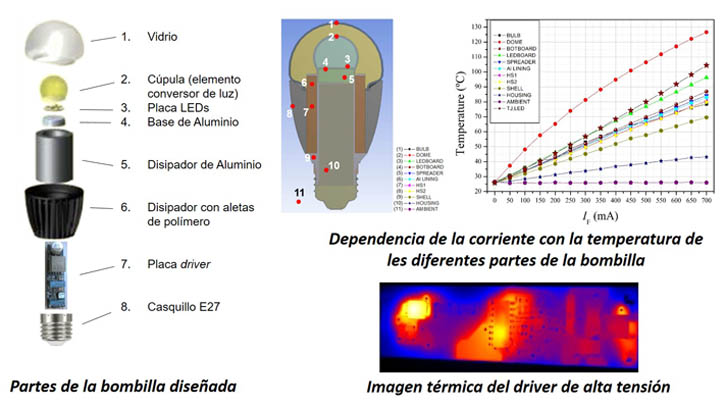
La iluminación de estado sólido (SSL, "Solid-State Lighting" en inglés) utiliza LEDs como fuente de luz. Esta aproximación empieza a ser omnipresente en nuestra vida diaria debido a los enormes beneficios que proporciona si se compara con otros tipos de iluminación como la de incandescencia, la de descarga o la de los fluorescentes compactos. La iluminación SSL ofrece una solución más sostenible, eficiente y con un claro impacto en el ahorro energético gracias a la buena eficiencia en la conversión de luz que proporcionan los LEDs: hasta un 40% de la energía eléctrica utilizada convierte en luz visible mientras que en una bombilla de incandescencia este valor es sólo del 15%. La eficiencia de la bombilla completa viene limitada también por la eficiencia de la electrónica necesaria para alimentar los LEDs (el llamado driver) y por los elementos ópticos que convierten la luz azul generada por los LEDs en luz blanca. Así pues, a pesar de una clara mejora de la eficiencia de las bombillas, aún generan una cantidad de pérdidas en forma de calor que hay que poder disipar al ambiente.
En este trabajo se han estudiado diversas estrategias para el diseño térmico de una nueva bombilla con el clásico casquillo de rosca E27 y con una alta capacidad lumínica (820 lm). Estas bombillas incorporan un driver, necesario para convertir los 220 V AC de la red a la corriente continua para alimentar la placa donde están los LEDs. Según la salida de este driver, se han analizado dos escenarios diferentes: el de baja tensión/alta corriente (18 V - 620 mA) y el de alta tensión/baja corriente (110 V - 85 mA). Para llevar a cabo este objetivo, ha sido necesario un diseño térmico de toda la bombilla LED y los drivers de control mediante herramientas de simulación multiescala, prestando especial atención a la integración del driver dentro del cuerpo de la bombilla. Gracias a los resultados de las simulaciones, se ha implementado y evaluado experimentalmente el nuevo diseño (el que se ve en la figura), que incorpora la esfera de cristal, el elemento conversor de luz (cúpula) y un disipador basado en un cilindro hueco de aluminio con unas aletas axiales de polímero de alta conductividad térmica, que permiten introducir el driver en el interior, con una base circular donde va montada la placa donde están los LEDs en la parte superior. Finalmente, en la parte inferior hay el tradicional casquillo de rosca E27.
Para evaluar térmicamente las bombillas, se han utilizado termopares y termografía infrarroja para obtener la distribución de la temperatura en la superficie del driver y en diferentes partes de la bombilla (ver foto). Se han hecho diferentes análisis comparándolos con una bombilla LED de referencia (Philips MASTERLED Glow lamp 6W). En primer lugar se ha utilizado una placa de LEDs como fuente de calor y sin considerar los drivers. Aparte de determinar las temperaturas en diferentes puntos clave de la bombilla como se ha dicho anteriormente, también se ha determinado la temperatura de unión de los LEDs gracias a un modelo térmico para ver el impacto de cada diseño en este parámetro. En segundo lugar, se han caracterizado los dos drivers con termografía IR para ver qué componentes se calentaban más en condiciones de operación. En tercer lugar, se han evaluado varias soluciones para mejorar la resistencia térmica de contacto entre la placa del driver y el disipador.
Desde el punto de vista de la implementación, el disipador propuesto permite obtener una reducción de la temperatura de unión del LED del 18% respecto a la bombilla de referencia. En cuanto a la comparativa entre drivers, el de alta tensión (110V) presenta temperaturas de sus componentes más bajas que las correspondientes al driver de baja tensión (18V). Por tanto, el driver de alta tensión es preferible en términos de eficiencia, tiempo de vida y fiabilidad, ya que permite la utilización de condensadores más pequeños y que no sean electrolíticos. En cuanto a minimizar la resistencia térmica de contacto entre el driver y el disipador, la mejor estrategia ha sido fijar la placa del driver con un material de interfase térmica (TIM) y rodeándola con un material de alta conductividad. En cuanto a las placas LED, la placa de alta tensión consume casi la mitad de la energía en la producción de luz en comparación con la de baja tensión, lo que hace que la solución de alta tensión merezca ser contemplada en los próximos años hasta que sus eficiencias sean comparables. De todos modos, la solución presentada permite utilizar cualquier tipo de placa LED aunque sea necesaria una producción de luz más grande ya que los drivers utilizados permiten suministrar la potencia eléctrica necesaria a los LEDs.
1Institut de Microelectrònica de Barcelona (IMB-CNM), Campus UAB, Barcelona
2Complex Materials, Eindhoven, The Netherlands
3Department of Microelectronics, Czech Technical University, Prague, Czech Republic
4Netherlands Organization for Applied Scientific Research, Eindhoven, The Netherlands
5Philips Lighting, Eindhoven, The Netherlands
Referencias
X. Perpiñà, M. Vellvehi, R. J. Werkhoven, J. Jakovenko, J. Kunen, P. Banken, P. J. Bolt and X. Jordà. (2019). Thermal Management Strategies for Low and High Voltage Retrofit LED Lamp Drivers. IEEE Trans. on Power Elect., vol. 34, nº 4, pp. 3677-3688, DOI: 10.1109/TPEL.2018.2853119.